How To Get the Right Plastic Extrusions for Your Product
Plastic extrusion involves melting raw plastic material, generally in pellet form. The molten plastic is then forced into a shaped opening in a die, which determines the final shape and size of the extrusion. This results in the formation of continuous profiles or shapes.
Seagate Plastics has over 35 years of industry experience providing high-quality solutions for various plastic needs. Our services include standard and custom extrusions, injection molded components, CNC machining, fabrication, and assembly. We also prioritize quality at every step of the process as an ISO 9001:2015 certified company.
Various Types of Plastic Extrusions and Their Applications
The versatility of the extrusion process allows for an array of shapes and sizes to meet specific product requirements across various industries. The most common forms of extrusions and their applications are as follows:
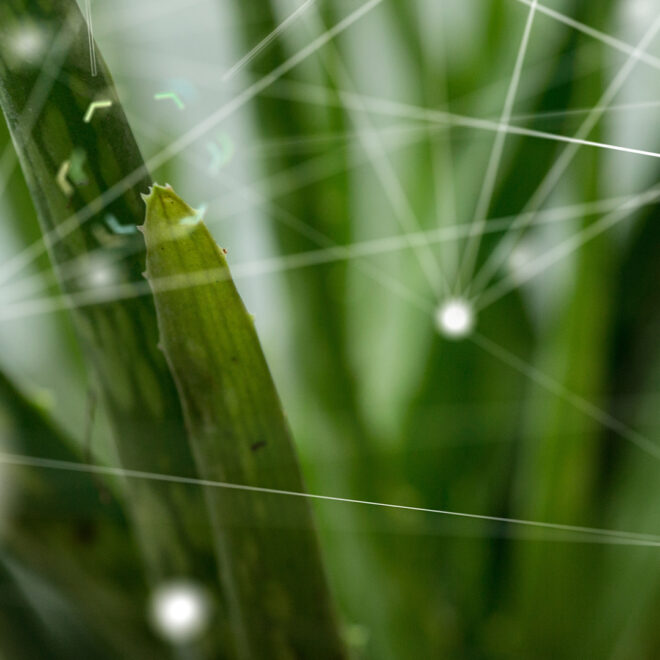
Pipe and Conduit Extrusions
Pipe and conduit extrusions are designed to create channels for fluid transportation or
wire management. Pipes transmit liquids or gases, while conduits serve as protective
pathways for electrical wires or cables. They often require jointing methods or fittings to
connect multiple sections or to adapt to different system requirements and applications.
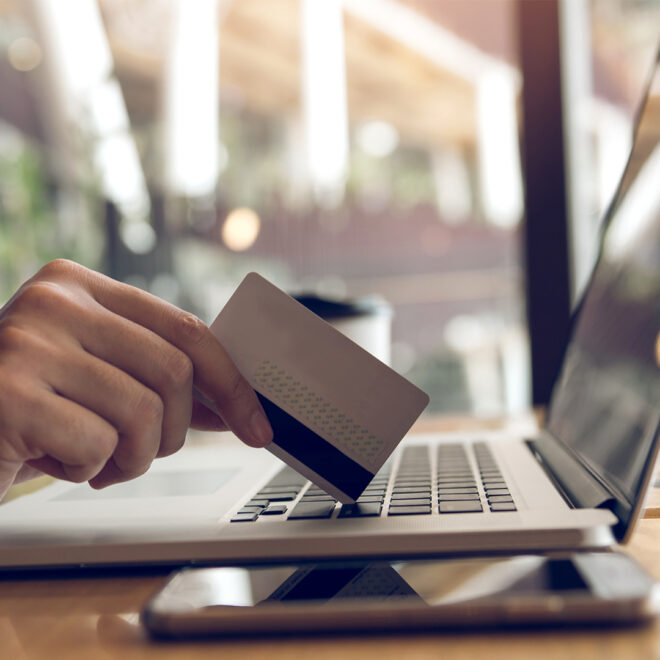
Profile Extrusions
Profile extrusions are known for their ability to create complex cross-sectional shapes. They can be designed to have varying forms, including square, rectangular, round, triangular, or custom profiles. Moreover, they often serve dual purposes by providing structural support and enhancing the product’s aesthetics. This makes them appropriate for construction and automotive applications.
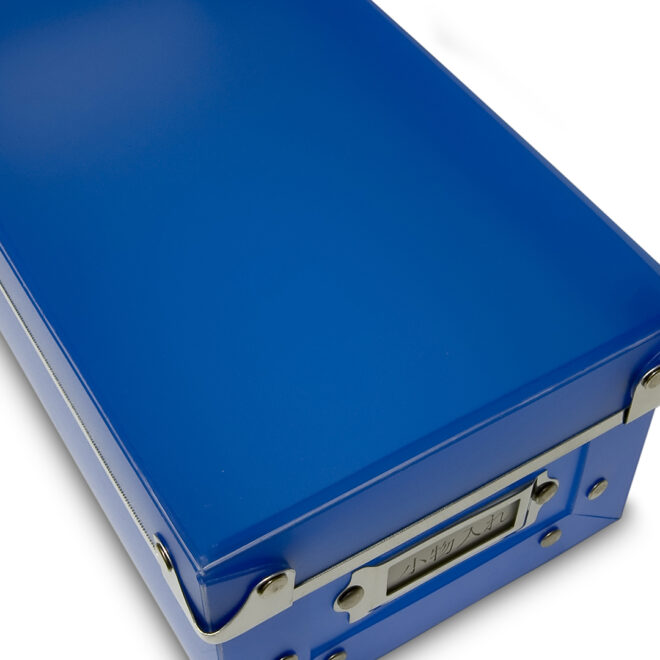
Sheet and Film Extrusions
Sheet and film extrusions produce thin, flat profiles with a uniform thickness. Sheets typically have a thickness of 0.25 mm or more, while films are even thinner – ranging from microns to a few millimeters. This characteristic allows for versatility in applications requiring a flexible, lightweight, or conformable material, such as packaging or wrapping.
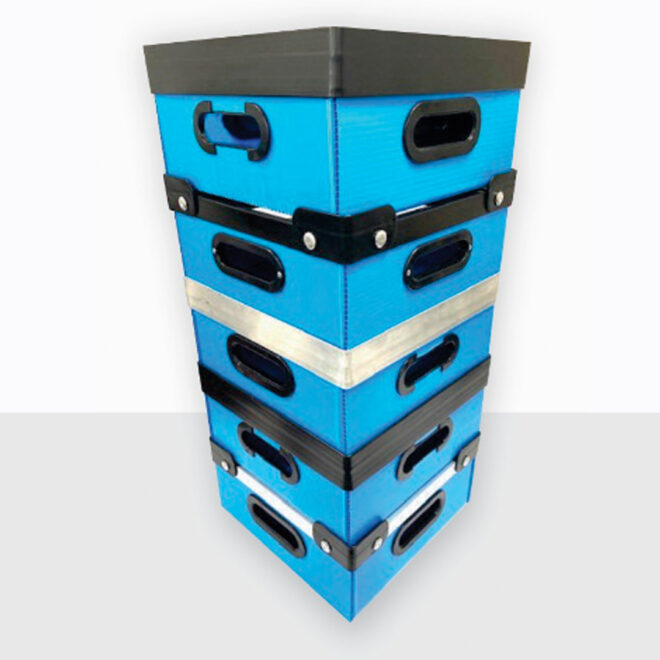
Tubing Extrusions
Unlike other extrusions that may have solid cross-sections, tubing extrusions are distinguished by their hollow center. This design enables the tubing to pass fluids, gases, or other materials. In addition, the open center provides functionality and versatility, making tubing extrusions suitable for applications like fluid transportation, wire management, and medical procedures.
Factors To Consider When Choosing Plastic Extrusions
When selecting the type of plastic extrusion for your application, it’s essential to consider various factors determining the method’s performance, functionality, durability, and cost-efficiency. Discussed below are the key aspects to keep in mind:
Material Selection
The choice of plastic material is crucial and depends on the specific application requirements. Consider chemical resistance, UV stability, mechanical properties, temperature tolerance, and industry standards or regulatory compliance. Different materials also offer varying properties that can impact the extrusion’s performance and longevity.
Examples of common plastic types for extrusion include the following:
- Acrylonitrile butadiene styrene (ABS)
- Polyvinyl chloride (PVC)
- Polyethylene (PE)
- Polypropylene (PP)
- High Impact Polystyrene (HIPS)
- Polyethylene terephthalate (PET)
- Polycarbonate (PC)
- Thermoplastic elastomers (TPE)
- ThermoPlastic Rubber (TPR)
Design and Profile Requirements
Determine the required shape, dimensions, tolerances, surface finish, and technical characteristics or functionality. Certain profiles or geometries may be more suitable for particular extrusion processes. For example, precision or tight-tolerance extrusion may enhance applications requiring exact dimensions and strict tolerances.
Application-Specific Properties
Properties such as hardness, flexibility, heat resistance, or antimicrobial properties should be evaluated based on the application’s specific needs. For instance, extrusions with good dielectric properties should be considered if electrical insulation is needed. In the case of fluid transportation, factors like pressure resistance, chemical compatibility, and flow characteristics of the extrusions become crucial.
The following are other examples of application-specific characteristics:
- UV stability
- Impact resistance
- Moisture resistance
- Abrasion resistance
- Transparency or opacity
- Color requirements
- Thermal conductivity
- Dielectric properties
Quality and Manufacturing Standards
Ensure the extrusion manufacturer adheres to high-quality standards and has a reliable manufacturing process. Look for companies that follow industry standards such as ISO certifications and have a record of producing high-quality extrusions. In addition, consider their expertise, experience, and industry reputation.
Cost and Lead Time
Evaluate the cost-effectiveness of the extrusions, considering both the upfront costs and the long-term benefits. Compare quotes from different manufacturers and assess the material costs, tooling costs, customization requirements, and potential volume discounts. Also, consider the lead time required for production and delivery, especially if the project has specific time constraints.
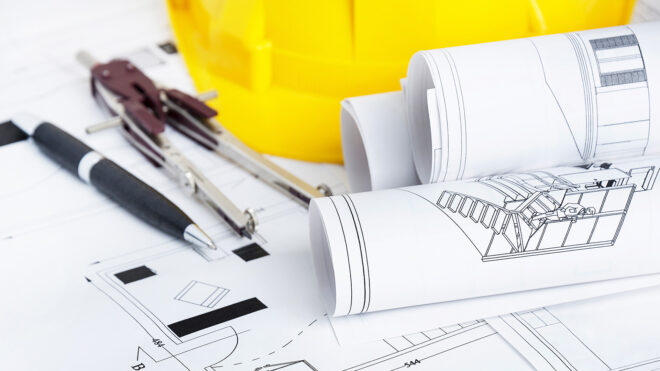
Tooling Design for Plastic Extrusion
The extrusion tooling, comprising the die and calibrators, is crucial in achieving precise control over the shape and dimensions of the extruded profile. The die design facilitates uniform flow distribution of the molten plastic material. Therefore, it should be carefully engineered to minimize flow disruptions, prevent warping and sagging, and ensure consistent material distribution throughout the profile.
On the other hand, calibrators cool and size the extrusion as it emerges from the die. Their design ensures consistent cooling and dimensional control, allowing the extrusion to achieve the desired dimensions and tolerances. Proper calibrator design includes considering cooling channels, surface textures, and geometries that aid in maintaining the required profile shape.
Tooling design considerations also include wall thickness, draft angles, and parting line location. The wall thickness should be designed to achieve the required functionality while avoiding issues such as sink marks or inconsistent thicknesses. Draft angles help extrusions slide out of tools without sticking or breaking. Lastly, proper parting line location facilitates assembly and post-extrusion processes.
Innovations and Trends in Plastic Extrusion Technology
The need for enhanced efficiency, sustainability, and advanced capabilities drives the evolution of plastic extrusion technology. Here are some noteworthy developments and trends in this field:
Advanced Material Formulations
There is a growing demand for extrusions made from advanced materials, such as bio-based polymers, recycled plastics, and composites. These materials offer improved sustainability, reduced environmental impact, and enhanced performance characteristics. Manufacturers are also developing new material formulations that exhibit properties like increased strength and higher heat resistance.
Advanced Material Formulations
There is a growing demand for extrusions made from advanced materials, such as bio-based polymers, recycled plastics, and composites. These materials offer improved sustainability, reduced environmental impact, and enhanced performance characteristics. Manufacturers are also developing new material formulations that exhibit properties like increased strength and higher heat resistance.
Advanced Material Formulations
There is a growing demand for extrusions made from advanced materials, such as bio-based polymers, recycled plastics, and composites. These materials offer improved sustainability, reduced environmental impact, and enhanced performance characteristics. Manufacturers are also developing new material formulations that exhibit properties like increased strength and higher heat resistance.
Advanced Material Formulations
There is a growing demand for extrusions made from advanced materials, such as bio-based polymers, recycled plastics, and composites. These materials offer improved sustainability, reduced environmental impact, and enhanced performance characteristics. Manufacturers are also developing new material formulations that exhibit properties like increased strength and higher heat resistance.
Trust Seagate Plastics for Your Custom Plastic Extrusion Solutions!
Seagate Plastics’ mission is to be the trusted one-stop shop for all your plastic extrusion and fabrication requirements. We offer a diverse range of top-quality manufacturing services, including custom and standard extrusions, injection molding, CNC machining, fabrication, and assembly. We utilize Master Cam software, allowing our team to convert mathematical data into programming efficiently and precisely.
today to discover how we can assist you! You can also now.